The process
Some of the secrets we’ve learned as we attempt to process flax fibre for linen
The magical transformation from field to fibre to linen makes for a regenerative and fully circular textile from Irish grown flax fibre. When we first planted some flax we did everything wrong. The wrong variety, the wrong seeding rate, we stored it badly, so many mistakes. Over the last six years we have learned so much, mostly from people with expertise, patience and generosity, also by gleaning old books and research. Below we’ve set out the process we’ve developed which works for us.
We can currently produce scutched fibre which can be hackled, spun and woven by hand or used for other non-spun purposes like composites. Our flax has also been used for making paper, wigs for giants for the movies, basket making, as a backdrop for photoshoots, for making a sporran, a plant medium, for raku firing and many other purposes.
Flax for linen traditionally takes 100 days to grow. We plant in early May. By mid July the first flowers appear and the field is absolutely buzzing with insects and flocks of linnets.
The crop doesn’t need any pesticides, herbicides, fungicides or fertiliser – no inputs at all other than sunshine and rain. We just leave it alone until it’s ready.
In Ireland they pulled it when it was two thirds yellow but in other parts of Europe including Courtrai, famed for it’s quality of linen, they pulled it earlier, just after the seed heads formed. You can read more about our sowing methods here.
Flax needs to be pulled rather than cut to preserve the length and quality of the fibre. Machinery for harvesting flax is widely available and used in Northern Europe however it’s not ideal for our hilly ground and current scale. The flax harvest has become the highlight of our year. Friends and family come to help and we camp out in the field. Every year we’ve got a little bit better at it.
Flax is pulled in large bunches – beets, and tied with rope before being stooked – about 12 beets to a stook.
We leave it in the field until it is nicely dried before bringing it in to store for the winter.
Retting is the process where bacteria breaks down the ‘gum’ that binds the fibre to the inner and outer core of the plant. Traditionally this was done in ‘lint holes’ or ‘flax dams’ – the flax was loaded into a pond and weighted down with stones. Talk to anyone who remembers flax being grown and they will tell you about the smell of the retting. There is a direct correlation between the rise of the Irish linen industry and the decline of river quality, this was due, in part, to nutrient rich retting water being allowed to run away into rivers. We worked closely with the Ballinderry Rivers Trust, an agronomist and a laboratory to be sure the system we use is river friendly. We rett in an upcycled cheese vat filled with harvested rainwater, we can ret about a tonne of flax in the vat and it takes around 10 days. Then the retting water is drawn out and is used as fertiliser on our fields, restoring the nutrients back to the soil. We leave buffer zones along the water ways so the nutrient is all absorbed by plants and can never reach the river. Getting the retting right is critical to the next stages so we keep a very close eye on it, checking 2 or 3 times a day. When it is ready we need to get it out straight away which is a real pain if it’s seven o’clock on a Saturday and you’ve been invited somewhere nice!Then it gets ‘grassed’, spreading it out on a mown field to dry, depending on the weather it may need turned several times before it gets retied and stored – again.
There are many versions of equipment used for breaking and scutching. We have 300 year old flax break which is on loan to us from Flaxmill Textiles. It is hand operated and we are told that this type of ‘machine’ was used in Ancient Egypt.
Then came water driven scutching turbines. One of the last still operating can be seen at McConville’s in Dromore, Co. Down
Then came belt driven turbines. We were lucky to find an old scutching turbine. It had been in use in Hardy’s Mill in Coagh up until the 1980’s, it had been stored, in bits, for about 40 years.
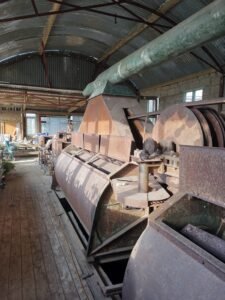
Looking back it’s hard to imagine why we thought it might be possible but Charlie has the heart of a lion and set about rebuilding this amazing machine.
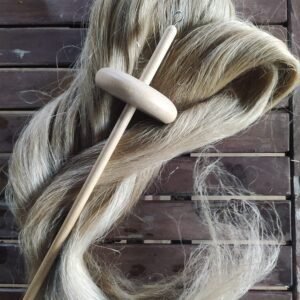
Once the fibre has emerged from the scutching machine, it can be combed to remove any remaining chaff. It’s just like combing tangled hair, starting at the ends and working back through a series of wide combs then progressively narrower. As it is combed it doesn’t just get cleaner, it gets smoother and shinier.
After heckling we are left with both fine line fibre and tow, in other words the long aligned fibres as well as the shorter fibres removed through the combing process. We can use both of these for spinning. Regine Neumann also showed us how to make paper from the tow.
In 2023 we started to sell scutched and hackled fibre to hand spinners and so far we’ve had some lovely feedback and lots of repeat orders.
Unfortunately we don’t have any flax spinning mills left in the UK or Ireland but we are hopeful that will change. The spinning of flax fibre is very different to wool, although it can be blended. The only place we know that is currently weaving with linen yarn grown and spun in Ireland is Flaxmill Textiles. They were shrewd enough to buy and store some of the last remaining stocks of yarn from the last of the Irish spinning mills as they closed down.
We are very lucky that we still have Irish Linen weavers here in Northern Ireland. Our first linen was produced on a handloom by master weaver Marion Bauer of Flaxmill Textiles.
Machine weaving is also a reality in Northern Ireland with companies like Thomas Ferguson and other members of the Irish Linen Guild.
Beetling is a finishing process which closes up the gaps in the weave and gives the fabric a sheen. It is achieved by hammering the linen with wooden posts over many hours. There is an old water powered beetling mill about 3 miles from our farm! Wellbrook Beetling Mill is owned by the National Trust and has open days throughout the year.
It is incredible that the last remaining commercial beetler is also nearby at Upperlands. William Clark & Sons is steeped in Irish Linen history. They have been kind enough to work with us on some early prototypes.
RESEARCH
We’ve provided links to some useful resources for researchers. Flax and other natural fibres are not new – they’ve been grown and processed for centuries. We encourage researchers to review the vast array of existing papers before embarking on new research.
Northern Ireland Natural Fibre Scoping Study, Prof Jane McCann: NFC Scoping Study NI 2019
Forgotten Books is an amazing resource, we especially love these titles:
- The Spinning and Twisting of Long Vegetable Fibres (Flax, Hemp, Jute, Tow,& Ramie) A Practical Manual of the Most Modern Methods as Applied to the Hackling, Carding, Preparing, Spinning, and Twisting, of the Long Vegetable Fibres of Commerce by Herbert R. Carter
- Flax and Hemp by Alexander Kirkwood
- Modern Flax, Hemp, and Jute Spinning and Twisting: A Practical Handbook for the Use of Flax, Hemp, and Jute Spinners, Thread, Twine, and Rope Makers by Herbert R. Carter
Flax Fibre for technical textile: A life Cycle Inventory Alejandra Gomez-Campos , Claire Vialle, Antoine Rouilly, Caroline Sablayrolles, Lorie Hamelin 2020
The Biology and Processing of Flax, H. S. Shekhar Sharma, C. F. van Sumere. M Publications, 1992